Design, lifestyle, and functionality are central purchasing criteria for sporting goods and accessories. For this booming market, many products are imported from Asia to Europe, which are not environmentally sustainable. Researchers at the Fraunhofer Institute for Chemical Technology ICT have developed an alternative.
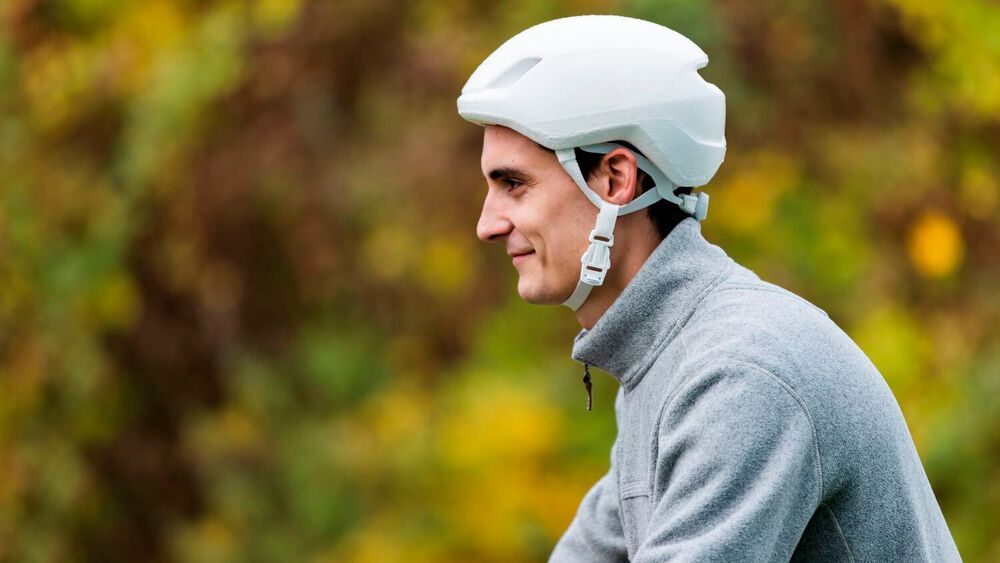
The product design of bicycle helmets rightly places functionality at the forefront. However, this has so far been at the expense of circularity, leaving a significant ecological footprint—especially when the helmets are made in Asia from mass-produced petroleum-based plastics: the helmet shell is made of polycarbonate (PC), the foam core of polystyrene foam (EPS), components often of polypropylene (PP), and straps of nylon (PA). Such a construction usually makes material recycling both technically and economically unfeasible at the end of the product’s life. As a result, helmets are typically incinerated after their three to five years of use.
Products made from mono-materials protect the environment
When questioning the principle of making each component from a material specifically intended for it, new, sustainable production approaches emerge. One such approach is demonstrated by the PIMMS project, funded by the Fraunhofer Future Foundation. Within its framework, various sports articles have been developed, consisting of only one material. According to the scientists, the bio-based and circular material PLA is particularly suitable. Thanks to its technical properties and competitive price, it has been established in the market for several years. Compared to the materials used so far, PLA has a material footprint up to eight times smaller.
Bicycle helmet is competitive
The bicycle helmet serves as a demonstrator for the new material and design concept, as it must ensure high functionality, particularly high energy absorption with low weight. Also crucial for market success are wearing comfort, price, and appearance.
As part of the one-and-a-half-year market-oriented project, Fraunhofer ICT, in cooperation with various industrial companies (Comfil ApS, Elas A/S, WSVK, Polyola SAS), developed particle foams, thermoforming films, fibers, and composites made entirely from PLA. Their production and processing require precise and individually tailored process control. Thanks to the broad collaboration, the PLA helmet could be manufactured in the same mass-production-capable process as the conventional petroleum-based bicycle helmet. This lays the foundation for a competitive market launch of the new helmets.
The material’s resistance to common environmental influences during use has already been positively tested. The standard-compliant external testing, which is intended to prove the helmet’s usability, is still pending. A lifecycle analysis (LCA) will also quantify the improved CO2 footprint of the recyclable mono-material bicycle helmet compared to the petroleum-based design throughout production, use, and end-of-life.
Post time: Jan-10-2025